Scredriving Bot 1
Project Duration: 6 weeks
Language Used: ROS2 Framework, c++, python
Library/Tool Used: MoveIt for ROS2 (Motion Planning Library), URDF (Robot Modelling), TF2 (ROS2 Transformation Library), Basic Computer Vision
3D Printing, end-effector design and Arduino integration (Completed single-handedly by Nick)
Co-author:
- Nicholas (James) Bell: Nick’s LinkedIn Profile
- Jiawen Zhang: Jiawen’s LinkedIn profile
Supervisor:
- Daryl Lee: Daryl’s LinkedIn profile
Open-sourced github repo: click_here
The project utilizes UR5e from Universal Robots for automated screw driving.
The novelty of this system lies in the integration of a depth camera mounted on the end effector, enabling the robot to adapt to different screw-hole locations without manual tuning.
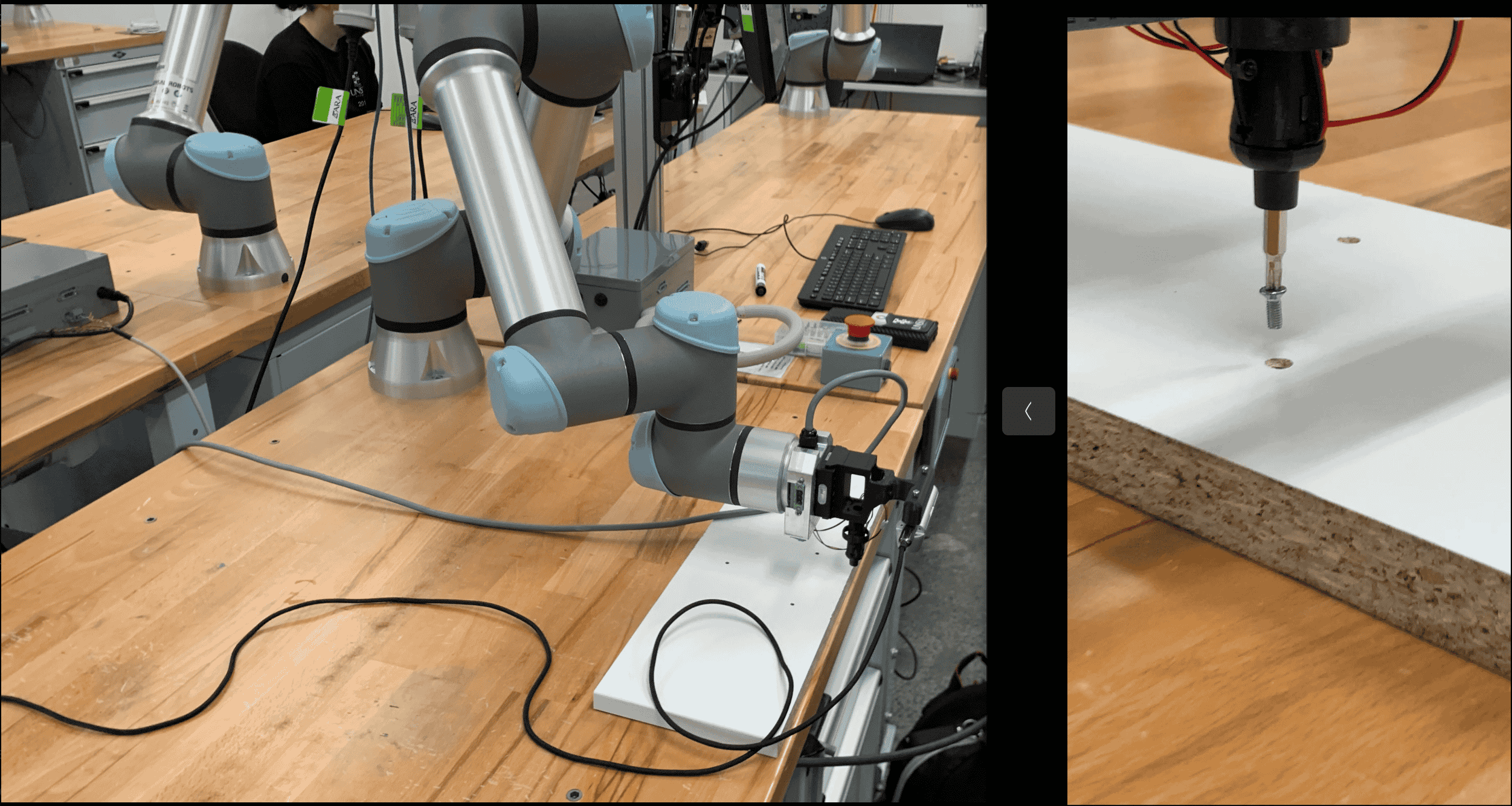
We won the 2024 UNSW MTRN4231 Course Competition
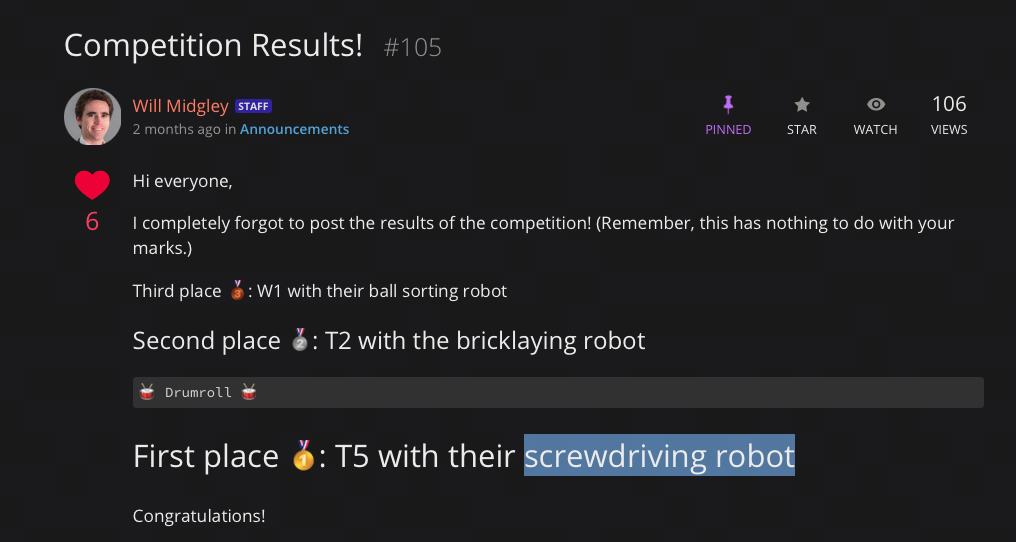
Graduate Thesis
Research Topic: Optimising Comprehensive Plant Data Collection Using a Mobile Manipulator for Holistic Agricultural Insights
Project Duration: 1 year (Ongoing progress)
Keywords: ROS2 Framework, C++, python, Modbus, Machine Learning (YOLO), Advanced Robotics Command Language (ARCL), Vision-based gripping, MoveIt!, Path Planning
Supervisor: Dr. Leo Wu
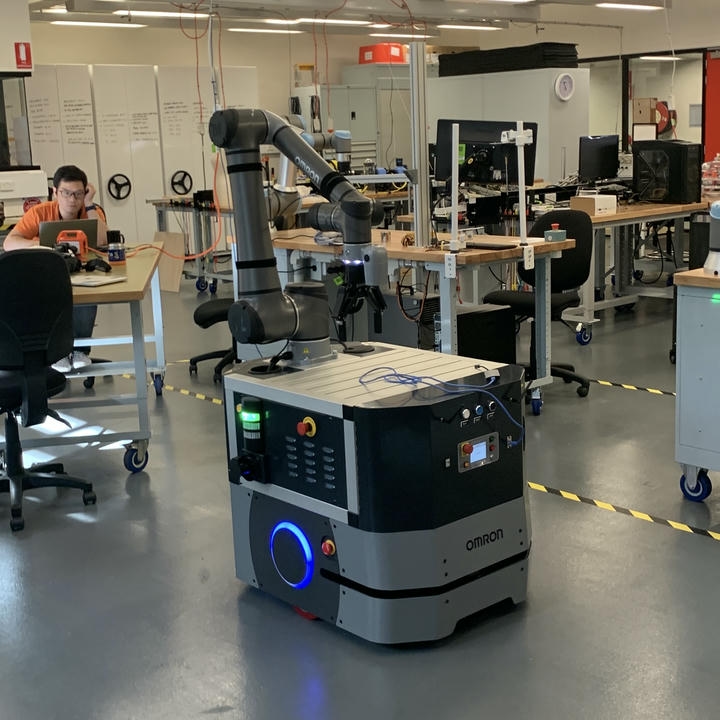
SIEMENS Process Simulate Plugins
Project Duration: 8 weeks
Language used: C#
Background: Process Simulate from SIEMENS is a software used by simulation engineers at FFT Shanghai to improve, verify and validate the correctness and plausibility of the welding production system design.
What does the plugin do: To improve effeciency by reduce repetitive work, I was assigned to design a plugin that generates a table showcasing the joint angles of the robot at each via-point. The plugin also highlights the via-points that are near joint limit or potential singularities.
Impact & Result:
- The plugin passed the internal screening and entered Alpha testing phase by the time I completed the internship.
- The plugins were described by the simulation team lead as “handy tools that will be used every day and save more than 3 hours on each project”.
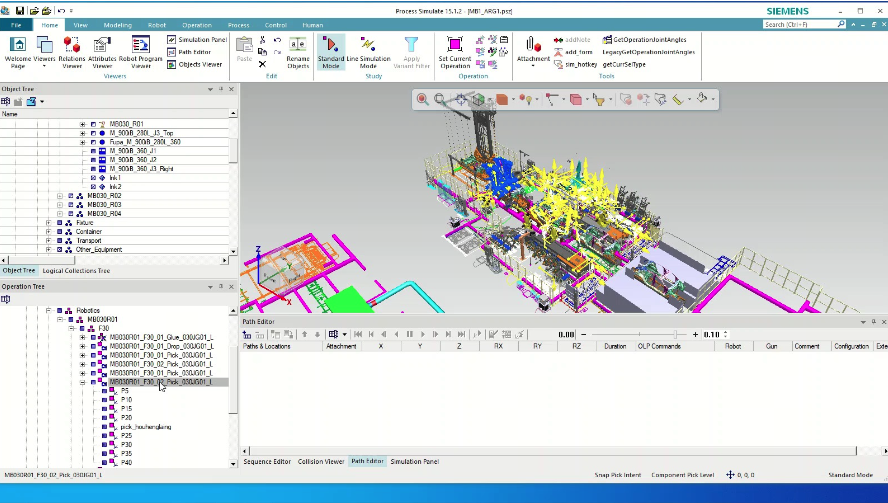
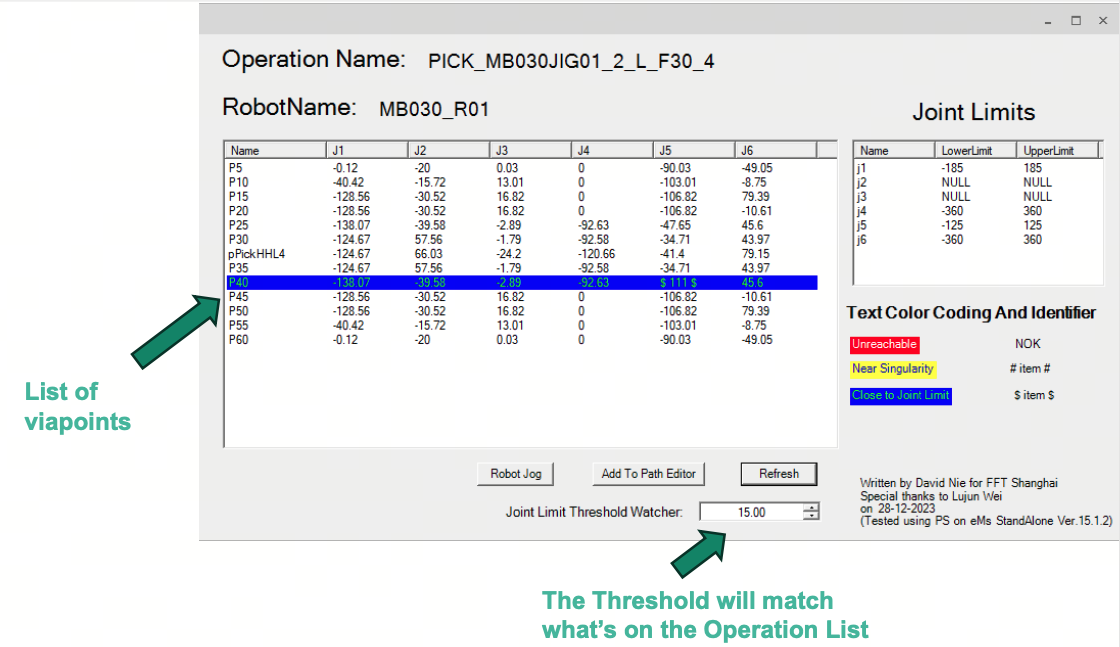
The Plugin Manual can be downloaded here